TM 1-1500-204-23-7
(e)
Leaks or through cracks. Defects of this type are cracks or openings which pass from one surface to
another.
(3)
False indications. False, or non-relevant, indications can appear to be actual defect Indications. The
typical ways that false indications occur are poor cleaning, press-fit, and poor developer removal
(a)
Poor cleaning. If all the surface penetrant is not completely removed in the washing or rinse operation,
the remaining penetrant may produce false indications. This is true for both the fluorescent (Type I) and visible dye
penetrants (Type II). Evidence of incomplete washing is usually easy to identify, since the penetrant will be in broad
areas rather than in the sharp patterns found in true indications. When accumulations of unwashed penetrant are found
on parts, these parts would be completely reprocessed In such cases, recleaning of the part before reprocessing is
recommended to remove all traces of surface penetrant.
NOTE
The danger of poorly washed parts lies in the fact that there may be actual cracks under the
improperly washed areas which are masked by the penetrant on the surface. A properly washed
part with no defects should have no areas of fluorescence, or random visible penetrant on it A
well processed part should show fluorescence or visible dye penetrant only at areas of the
defects.
(b)
Press-fit parts. A condition which may create false indications is when parts are press-fitted into each
other. If a wheel is press-fitted onto a shaft, penetrant will show an indication at the fit line. This is perfectly normal since
the two parts are not welded together The only problem with such indications is that penetrant from the press-fit may
bleed out and mask a true defect.
CAUTION
Where penetrant bleed out may mask defects on press-fit parts, the time between application of
developer and inspection should be held to a minimum to prevent excessive bleed out.
(c)
Developer removal. Sharp fillets, threads, and keyways will often retain penetrant at the base despite
a good washing removal technique, and give indications. This is particularly so when Type I or 1, II, Method B is
employed. Because heat-treating or fatigue cracks often do occur at such locations It is essential that the inspector
check these locations very critically.
3-13. Types of Fluorescent Penetrant Processes. There are three general types of penetrant inspection processes
These are known as type I, type II, and type Ill. Type I processes use fluorescent penetrants, type II uses visible
penetrants and type III uses visible and fluorescent penetrant (dual mode). Within each type, there are four methods of
removal known as method A, B, C, and D Table 3-2 list the various types and methods of penetrant inspection.
CAUTION
The Army prohibits the use of dual mode (visible and fluorescent) and visible dye penetrants on
aircraft, engine, and missile parts except for those with specific engineering approval.
3-14. Type I, Method C Penetrant Inspection. The type I, Method C inspection process for use In field (portable)
operations is a penetrant Inspection using a fluorescent dye with nonaqueous developer and solvent remover It can be
used in a field (portable) operation and is described in the following paragraphs.
a.
Precleaning Process. The precleaning process makes the part or item clean and free from foreign matter that
may cover or confuse the indications. Effective cleaning methods that may be employed to remove soils or
contaminates from the surfaces of parts and defects are as follows:
(1)
Alkaline cleaning. Alkaline cleaners are nonflammable water solutions containing specially selected
detergents for wetting, penetrating, emulsifying, and saponifying various types of soils When thoroughly used, they leave
a water-break-free surface which is both chemically and physically clean. Due to their special wetting and dissolving
powers, they also pull contamination from the flaws, thus preparing them to absorb the dye penetrant
(2)
Water cleaning with detergents. Washing machines using hot water and detergents may be used to clean
parts. The use of this method, however, will depend greatly on the type of soil present. Oil and grease-filled defects may
not be satisfactorily cleaned by this method.
3-13
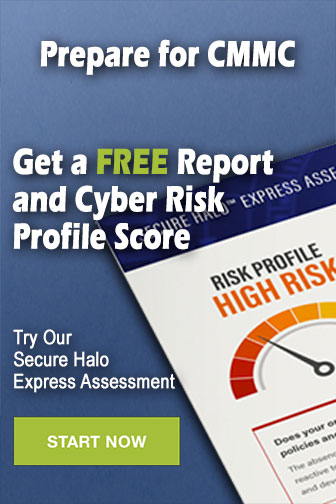