TM 1-1500-204-23-7
4-4. Fundamentals of Magnetic Particle Inspection. Magnetic particle inspection is a method of nondestructive
testing which uses very small magnetic particles to reveal discontinuities in parts capable of being magnetized. It reveals
surface, and near subsurface, discontinuities in parts made of magnetic substances. It consists of three basic operations.
Establishment of suitable magnetic field.
Application of magnetic particles.
Examination and evaluation of the particle accumulations.
4-5. Capabilities and Limitations. Magnetic particle inspection can detect discontinuities in parts made of magnetic
substances. If the part is made from an alloy which contains a high percentage of iron and the part can be magnetized, it
is in a class of metals called ferromagnetic and it can be inspected by this method If the part is made of an element
which is non-magnetic, it cannot be inspected by this method. The magnetic particle inspection method will detect
surface discontinuities including those that are too fine to be seen with the naked eye, those that lie slightly below the
surface, and when special equipment is used, the more deeply seated discontinuities.
4-6. Inspection Preparation. Parts or surfaces should be clean and dry before they are subjected to any magnetic
particle inspection process. The cleaning process used must not affect the part in any way that will reduce the
effectiveness of the inspection process. The cleaning process is required to remove all contaminants, foreign matter and
debris that might interfere with the application of current or the deposit of the magnetic particles on the test surface.
4-7. Particles and Methods of Application. The particles and their methods of application in magnetic particle
inspections are covered in the following paragraphs.
a.
Particles. Particle composition and sizes are explained in the following paragraphs.
(1)
Particle composition. The particles used in magnetic particle testing are made of magnetic elements,
usually combinations of iron and iron oxides, having a high permeability and low retentivity. Particles having high
permeability are easily magnetized by and attracted to the low-level leakage fields at discontinuities. Low retentivity is
required to prevent the particles from being permanently magnetized Strongly retentive particles tend to cling together
and to any magnetic surface, resulting in reduced particle mobility and increased background accumulation.
(2)
Particle sizes. Particle sizes are very small ranging from about 0 0002 inch to 0.0006 inch in commonly
used formulations. Each magnetic particle formulation always contains a range of sizes and shapes to produce optimum
results for the intended use. The smallest particles are more easily attracted to and held by the low-level leakage fields
at very fine discontinuities; larger particles can more easily bridge across coarse discontinuities where the leakage fields
are usually stronger. Elongated particles are included, particularly in the case of dry powders, because these rod-shaped
particles easily align themselves with leakage fields not sharply defined such as occur over subsurface discontinuities.
Globular shapes are included to aid the mobility and uniform dispersion of particles on a surface.
b.
Methods of Application. Magnetic particles may be applied as a dry powder or wet, using either water or a high
flash point petroleum distillate as a liquid vehicle carrier. Dry powders are available in various colors so the user can
select the color which contrasts best with the color of the surfaces upon which they are used. Colors for use with ordinary
visible light are red, gray, black or yellow. Red and black colored particles are available for use in wet baths with
ordinary light and yellow-green fluorescent particles for use with black light. Fluorescent particles are widely used in wet
baths since the bright fluorescent indications produced at discontinuities are readily seen against the dark backgrounds
which exist in black light inspection areas.
(1) Dry powder application. Dry powder can be applied by hand and compressed air guns. Each is explained
in the following paragraphs.
(a)
Hand application. Magnetic particles in dry form may be applied by hand using rubber squeeze bulbs
or plastic squeeze bottles equipped with perforated caps similar to an ordinary salt shaker but with smaller holes. The
objective is to lay down a light cloud of powder on the part being inspected, this is usually accomplished by using a
combination of bulb squeezing and tossing the powder toward the area being inspected.
WARNING
Never point a compressed air tool at another person. Airborne particles may cause blindness or
serious injury.
4-2
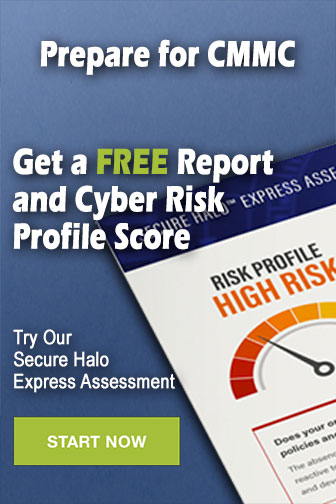