TM 1-1500-204-23-7
(6)
Solvent cleaning. Solvent-type cleaners can be specially selected for wiping parts when vapor degreasing
equipment, alkaline hot tanks, and steam cleaning equipment may not be available. The solvent may be applied by hand
but care must be taken to ensure that all defects and surfaces are free from contamination.
(7)
Mechanical cleaning. Abrasive blasting shall be used to clean metals only if the surface of the metal is not
peened by the process or if surface defects are not sealed or contaminated with the abrasive material.
(8)
Paint removal. Paint shall be removed by the application of an approved paint stripper using
recommended instructions Paint films can be removed by bond-release, solvent paint strippers, or dissolving type hot-
tank paint strippers In all cases the paint film must be completely removed down to the surface of the metal.
b.
Application of Cleaner. When the precleaning process is chosen, follow the appropriate maintenance manual or
manufacturers instructions when applying the cleaner.
c.
Penetrant Application. Type I penetrants can be applied by dipping, flow-on, spraying, brushing, or any method
which completely covers the area of inspection.
(1)
Dipping. In the dipping method of application, the part, or basket of parts, is dipped into the applicable
solution. Dipping is generally preferred in hand operations and is used for applying penetrants, emulsifiers, and aqueous
wet, and dry developers to the part or material under test.
(2)
Flow-on. In the flow-on method of application, the applicable solution Is poured or flowed on the part or
material under test. Flowing on the solution is generally preferred in automatic equipment operations, and is used for
applying penetrants, emulsifiers, and aqueous wet developers to the part or material under test
(3)
Spraying In the spraying method of application, the applicable solution is sprayed on the part or material
under test using a spray gun or pressurized cannister. Spraying can be used in hand or automatic equipment operations,
and is used for applying penetrants, emulsifiers, and is the best method for applying aqueous and non-aqueous wet
developers to the parts or material under test.
(4)
Brushing. In the brushing method of application, the applicable solution is applied with a brush. Brushing
is used only in hand operations, and is used for applying penetrants.
d.
Removal of Excess Penetrant. After the penetrant dwell time is completed, the excess penetrant shall be
removed by hand wiping with a dry, lint-free cloth.
e.
Application of Developer. This group of penetrants carry only nonaqueous wet developers. The nonaqueous wet
developer only should be used for stress or intergranular corrosion defect because of its high degree of penetrant
occurancy. Apply the nonaqueous wet developer as follows:
(1)
Prior to application, mix developer thoroughly.
(2)
Apply developer using the spray method whenever possible, otherwise use brushing method. Spray gun
can be vibrated to increase sensitivity.
(3)
Drain developer and allow for developer dwell time.
f.
Inspection of the Part. Follow procedures in paragraph 3-12a to inspect the part.
g.
Evaluate Discontinuity. Follow procedures in paragraph 3-12b to evaluate and interpret the discontinuity.
h.
Removal of Developer. Follow the procedures In paragraph 3-14a to remove the developer prior to returning a
serviceable part to service. It is just as important to remove all of the developer after inspection as it was to remove all
dirt and grime prior to inspection.
3-15/(3-16 blank)
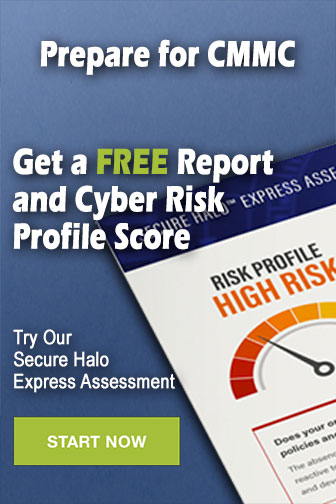