TM 55-4920-328-13
starter and contactor compartment in the control cab
module to supply 208v ac, three-phase electrical power
to the pump motor in the oil system. The pump
operates to supply turbine lubricating oil to the T53 and
T63 engine through the manual valve and 40-micron
filter. The oil flows through the check valve to the
engine under test at a pressure not to exceed 2 psig.
The relief and bypass valve, set at 35 psig, allows
excess oil in the supply line to return to the oil reservoir.
Scavenge oil from the engine flows through the heat
exchanger and across the temperature probe to a three-
position manual selector valve. The T74 engine is
provided with a self-contained oil system, but requires
external oil cooling. The center position of the manual
selector valve diverts cooled engine system oil from the
heat exchanger to return to the engine through the oil
system supply line and 40-micron filter. The T53 engine
position of the manual selector valve allows scavenge
oil to return to the oil reservoir through a back pressure
regulating valve set at 55 to 60 psig. The T63 position
of the manual selector valve allows scavenge oil to
return to the tank through a second back pressure
regulator set at 30 psig. The temperature regulating
valve, actuated by the temperature probe, is set at
180°F to regulate the flow of cooling water through the
heat exchanger to maintain a constant oil temperature.
Engine gearbox oil vapor returns to the tank assembly
through another return line. When the supply oil level
drops to a point six inches or less from the bottom of the
tank assembly, the fluid level transmitter operates to
complete a circuit to energize the ENGINE LOW OIL
LEVEL indicator DS10 (17, figure 1-25) on the upper
panel of the services sub-module.
(8) Portable oil lubricating unit pumping assembly.
(a) The portable oil lubricating unit pumping
assembly (figure 1-14), hereinafter referred to as the
portable oil unit, provides low-pressure lubricating oil for
lubrication of the bearings on certain water brake
assemblies. The portable oil unit is an enclosed
assembly
(shown
schematically
in
figure
1-15)
consisting of a rectangular oil tank (1, figure 1-14),
motor, supply pump, scavenge pump, heat exchanger,
and relief valve. Two pressure gages (4,5), a 10-micron
filter, and a flow switch are installed in the pressure line
to the supply port. A pressure switch is also connected
to the supply line to provide a low oil pressure warning
to the test technician. The portable oil unit is equipped
with a combination oil tank cap and filter-breather (2),
sight indicator (3), electrical receptacles (6. 9. 12) for
Dower and signal circuit connections, oil out and return
fittings (7,8), and heat exchanger cooling water in and
out fittings (10,11). The motor is a 208v ac, three-
phase, 60 Hz unit used to simultaneously drive the
supply and scavenge pumps.
(b) With system power from the generator
set available at the control power module (Unit 5), the
INST PWR ON switch S1 (7, figure 1-26) is energized.
The LUBE PUMP START switch S13 (13) is then
depressed to energize the coils of the contactors in the
starter and contactor compartment in the control cab
module to supply 208v ac, 60 Hz power to operate the
motor and drive the pumps. The relief valve is set to
open at 20 psig to bypass supply oil to the tank
assembly to prevent excessive pressures to the water
brake bearing. The pressure gages installed in the
supply line indicate the amount of pressure drop across
the filter. The differential pressure indicates the amount
of clogging in the filter and is used as an indication of
the need for cleaning. At a flow above 0.25 gpm, the
normally-closed spat flow switch is in the open position.
When the flow rate drops below the specified value, the
flow switch closes to complete a circuit and illuminate
the WATER BRAKE LOW OIL FLOW indicator DS6
(22, figure 1-25) on the ALARM DISPLAY section of the
upper
panel
in
the
services
sub
module
and
simultaneously cause the audible alarm to sound. The
spat pressure switch is in the normally-closed position at
normal supply pressures. When the supply pressure
drops below a pre-set pressure of 12 to 13 psig, the
switch actuates to complete a circuit to illuminate the
WATER BRAKE LOW OIL PRESS indicator DS4 (20)
on the panel and simultaneously cause the audible
alarm to sound. If a warning light comes on and the
audible alarm sounds, the LUBE PUMP STOP switch
S14 (25, figure 1-26) on the No. 1 power control panel
assembly (32) is depressed to stop the motor and
pumps. Refer to table 1-1 for additional leading
particulars of the portable oil unit.
(9) Test trailer water system.
(a) The test trailer water system (figure 1-
16) provides cooling water for METS systems. The test
trailer water supply system (shown schematically in
figure (17) consists of a series of plumbing lines
connected to a 0.125-inch mesh strainer (2, figure 1-16),
inlet control valve (15), 75-micron filter (5), two flow
switches (4, 6). back pressure control valve (13), quick-
disconnect fittings and the T700 water filter with 21
changeable elements, all located below the test trailer
deck. The filter and flow switches control the supply of
water to the water brake bearing. The inlet control valve
and back pressure control valve are both hydraulically
1-18 Change 3
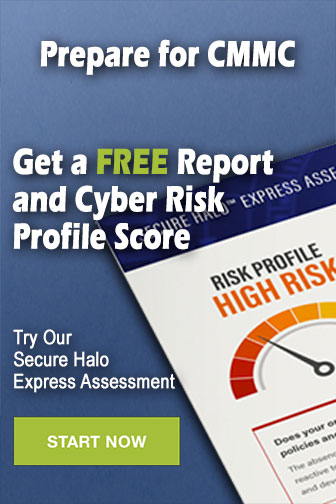