TM 55-4920-328-13
four flush-mounted retaining screws. Cutouts in the
front panel mount the following back-lighted switches,
depicted in figure 1-26:
INST PWR S1 (7), S2 (31)
Brake Pump S3 (8), S4 (30)
Cooling Pump S5 (9), S6 (29)
Tower Fan No. 1 S7 (10), S8 (28)
Tower Fan No. 2 S9 (11), S10 (27)
Air Comp S11 (12), S12 (26)
Lube Pump S13 (13), S14 (25)
Oil Pre-Heat S15 (14), S16 (24)
Oil Pump S17 (15), S18 (23)
Fuel Pump S19 (16), S20 (22)
Flood Lights S21 (17), S22 (21)
Beacon S23 (19), S24 (20)
Left Console Fan S25 (6)
Right Console Fan S26 (18)
The upper row of 12 switches across the lower front
panel of the No. 1 power control panel assembly are
placarded ON or START as appropriate. These guarded
switches are identical in design and function. Each
switch is a spdt, red lens, pushbutton type unit with a
continuous service rating of five amperes and having
0.25 inch of travel. The lower row of 12 switches are
placarded OFF or STOP, as appropriate. These
guarded switches are similar to the top row of switches
except that each lens is green. The chassis assembly
also mounts six relays: K1, K2, K3, K4, K5, and K6.
The under frequency relay (76, figure 719) will actuate
causing the system to shut down should the input power
frequency fall below 55 Hertz. An over voltage
protection system consisting of a voltage sensitive relay
(27C, figure 7-19) is incorporated. This relay, adjustable
from 92V to 140V, is deenergized while the voltage is
maintained within normal limits and energized at the
over voltage condition. All power to the motors and
consoles except the water pump motor and lube oil
pump motor will be cutoff when the relay is energized.
Power can be manually restored to the system when the
voltage drops below the maximum set point. Terminal
board assembly TB1 is installed in the lower panel of the
chassis assembly. The rear panel provides a mounting
for five connectors J1 through J5.
(j) Left hand castle assembly (Unit 8).
The left hand castle assembly 8A1 (14, figure 1-21),
installed
in
the
control
cab
assembly,
consists
essentially of a blower 8A1 mounted in a rectangular
castle assembly. Five Blank filler panels are mounted
on the front of the castle assembly, immediately below
the blower, by the use of 20 sets of receptacles,
retainers, and screws. The castle assembly is a sheet
metal structure 22.00 inches, TM 55-4920-328-13
wide, 27.56 inches high, and 16.38 inches deep.
The blower (8A1) (1, figure 7-20) is a standard 19inch
rack-mounted chassis provided in the left hand castle
assembly to provide forced air or exhaust ventilation for
the control cab module, depending on the mode of
installation. The blower will selectively deliver 100 or
200 cfm of air in either mode. The unit utilizes an 8-
inch, dynamically balance, squirrel cage wheel driven by
a 1/20horsepower motor powered by 117v ac, threewire,
single-phase, 60 Hz power. Two motor speeds are
available by use of a speed selector switch. The unit is
equipped with an oil-impregnated fiberglass filter.
Intake or exhaust air, as determined by the mode of
installation, passes through a chrome-plated grill.
(k) Right hand castle assembly (unit
9).The right hand castle assembly 9A1 (figure 1-27) is
installed in the control cab assembly opposite to the left
hand castle assembly. The castle assembly utilized in
this unit is essentially identical to that used in Unit 8,
except for the panel-mounted components. The right
hand castle assembly is equipped with a blower 9A1 (1),
identical to the Unit 8 blower, a filler panel (2), a
pneumatic control assembly 9A2 (10), and an ancillary
panel assembly 9A3 (3). These panel assemblies are
secured to the front cutout portion of the enclosure with
12 sets of receptacles, retainers, and flushmounted
screws.
1. Pneumatic control assembly 9A2. The
pneumatic control assembly (10, figure 1-27) is chassis-
mounted assembly consisting essentially of an AIR
SUPPLY switch (9), air pressure gage (8), solenoid
valve (34, figure 7-21), pressure regulator (6, figure 1-
27), electrical wiring, plumbing runs, and hose
assembly. A connector J1 and a chassis ground stud El
are installed on the rear panel of the chassis assembly.
a.
Air pressure gage. The air pressure gage (8,
figure 1-27) is a conventional Bourdon tube pneumatic
gage having a full scale range of 0 to 160 psig, with the
dial graduated in 10-psi increments. Three screws
secure the flange of the gage to the front panel of the
pneumatic control assembly (10). The pressure
connection located on the rear face of the housing
accommodates a 1/8-27 NPT adapter for connection
into the pneumatic circuit.
b.
Solenoid valve. The solenoid valve (34, figure
Z-21) is a normally-closed, solenoid-operated valve
used in the air system. Operation of the valve is
controlled by the AIR SUPPLY switch (9, figure 1-27).
When the switch is positioned to ON, 28v dc electrical
power
is
made
1-53
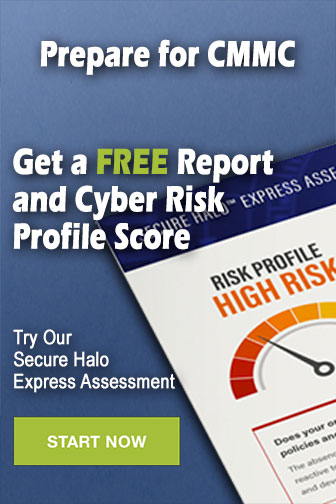