TM 1-1500-204-23-1
Table 9-1. Cable Damage Limits
Cable type
Allowable broken wire
7x7 (flexible)
2 per inch of strand, provided not more than 3
exist in that inch of cable
7x19 (flexible)
3 per inch of strand, provided not more than 6
exist in that inch of cable
1x19 (nonflexible)
None
(d) If the surface of the cable is
corroded, relieve cable tension and carefully force the
cable open by reverse twisting. Visually inspect the
interior.
NOTE
Corrosion on the interior strands of
the cable constitutes failure, and the
cable must be replaced
(e) If no internal corrosion is
detected, remove loose external rust and corrosion with
a clean, dry, coarse-weave rag or fiber brush. After
thorough cleaning, apply corrosion preventive, MIL-C-
16173 Grade 2, sparingly. Do not apply the material so
thick that it will interfere with the operation of cables at
fairleads, pulleys, or grooved bellcrank areas.
NOTE
Do
not
use
metallic wools
or
solvents to clean installed cables.
Use of metallic wool will imbed
dissimilar metal particles in the
cables and create further corrosion
problems. Solvents will remove
internal
cable
lubricant
allowing
cable strands to abrade and further
corrode.
(3)
Control cable tension adjustment. Rig
aircraft
as
outlined
in
the
applicable
aircraft
maintenance manual. After rigging, measure for proper
tension on control cables, using a tensiometer. Use the
following procedures to measure cable tension.
(a)
Place cable under the two
blocks on instrument, and pull lever on side of
instrument down. This pushes up on the center block,
called a riser. The force required to raise the center
block is indicated by a pointer on the scale.
(b)
Convert
indicator
reading
to
tension pounds (see figure 9-22).
(c) Adjust cable tension to proper
value by either tightening or loosening turnbuckles.
(4)
Control cable emergency repair. If
possible, duplicate spare cables should be used for
replacement. When spare cables are not available and
immediate replacement is imperative, use one of the
following methods of splicing.
CAUTION
Care must be taken that splice does
not foul fairlead or pulley, nor in any
other way prevent proper movement
of the cable
(a) Woven spliced terminals. Use
woven spliced terminals on cables 3/32 inch diameter or
greater in place of swaged terminals. Fabrication
components needed are shown in table 9-2. Perform
the following procedures to fabricate woven spliced
terminals:
1 Sweat solder or wrap cable
prior to cutting to prevent fraying.
Table 9-2. Fabrication Components
Nomenclature
Specification
Cable, corrosion-resistant
MIL-W-83420
Wire rope, 1 tinned steel
MIL-W-83420
Cord, serving
V-T-291
Solder, tin-lead
QQ-S-571
9-18
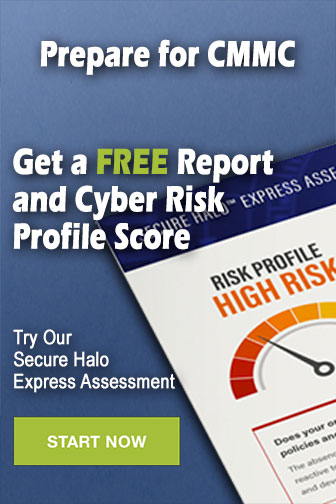