TM 1-1500-204-23-1
f.
Control System Components. Control
system components are explained in the following
paragraphs.
(1)
Turnbuckles. A turnbuckle assembly
is a mechanical screw device consisting of two threaded
terminals and a threaded barrel. Figure 9-25 shows a
typical turnbuckle assembly. Turnbuckles are fitted in
the cable assembly for the purpose of making minor
adjustments in cable length and for adjusting cable
tension. One of the terminals has right-hand threads
and the other has left-hand threads. The barrel has
matching right- and left-hand internal threads. The end
of the barrel with the left-hand threads can usually be
identified by a groove or knurl around that end of the
barrel.
(a)
Turnbuckle replacement criteria.
Replace turnbuckles and turnbuckle barrels that are
cracked, corroded, or have stripped threads.
(b)
Turnbuckle
tolerances.
Turbuckle tolerances are three visible male (cable
terminal) threads or four visible female (turnbuckle
barrel) threads, each of which should be free of
evidence of corrosion at the root of the threads. (The
maximum of four visible female (turnbuckle barrel)
threads applies only to initial installation of the cable, so
that if the cable stretches, the turnbuckle can be
adjusted to the desired cable tension, at which time,
more or less than four barrel threads may be exposed.)
Safety all turnbuckles.
(2)
Cable terminals. Terminal fittings are
generally of the swaged type. They are available in the
threaded end, fork end, eye end, single-shank ball end,
and double-shank ball end. The threaded end, fork end,
and eye end terminals are used to connect the cable to
a turnbuckle, bellcrank, or other linkage in the system.
The ball-end terminals are used for attaching cables to
quadrants and special connections where space is
limited. Figure 9-26 shows the various types of terminal
fittings. Visually inspect and replace clevis or terminals
that are scratched, nicked, dented, corroded, have
stripped threads, or are found bent (distorted).
NOTE
Minor nicks, scratches, corrosion
pits, less than 0.005 inch deep, may
be
removed
by
cleaning
and
burnishing smooth, to restore the
part to useful service.
(3)
Fairleads. Fairleads, as shown in
figure 9-27, are used to guide cables in a straight line
through or between structural members of the aircraft.
Inspect
fairleads
for
wear,
breakage,
alignment,
cleanness, and security. Examine cable routing at
fairleads to assure that deflection angles are no greater
than 3 degrees maximum. Determine that all guides
and anti-abrasion strips are secure and in good
condition. Replace rubber or nylon grommets that show
evidence of excessive wear. Replace worn or cracked
phenolic fairleads. Reposition fairleads that allow
cables to chafe.
(4)
Pulleys. Pulleys are used to guide
cables and change the direction of cable movement.
Various cable system malfunctions may be detected by
analyzing
pulley
conditions
These
include
such
discrepancies as too much tension, misalignment, pulley
bearing problems, and size mismatches between cables
and pulleys. Examples of these conditions are shown in
figure
9-28
inspect
pulleys
using
the
following
procedures:
(a)
Reposition pulleys that do not
align with cables within 2 degrees. Replace inoperative
or other- wise defective pulleys.
(b)
Inspect pulleys for roughness,
sharp
edges,
and
presence
of
foreign matenal
embedded in the grooves.
(c)
Inspect pulleys for excessive
grooving by visual examination of the surface, and by
rotating pulley and observing if the cable twists, rotates,
or jumps up and down, as a result of interplay between
the grooves of the pulley and the lay of the cable.
(d)
Examine
pulley
bearings
to
assure proper lubrication, smooth rotation, freedom from
flat spots, dirt, and paint spray. Inspect pulley bearings
for roughness, binding, noise, rust, lubricant leakage,
and excessive looseness compared to a new bearing.
(e)
Maintain pulley alignment to
prevent the cable from riding on the flanges and chafing
against guards, covers, or adjacent structure.
(f)
Check all pulley brackets and
guards for damage, alignment, and security. Replace if
cracked, corroded, or otherwise damaged.
(g)
Periodically
rotate
pulleys,
which turn through a small arc, to provide a new bearing
surface for the cable.
9-24
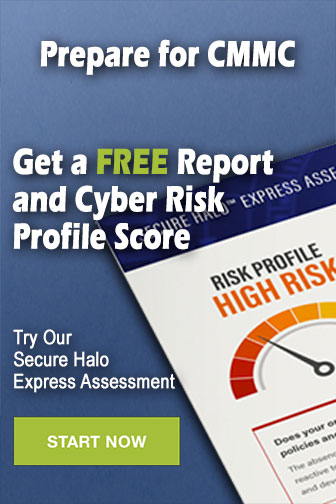