TM 1-1500-204-23-2
e.
Air Filters. An air filter is usually located in the line leading into the system supply source. Additional
filters may be located at various points in the system lines to remove any foreign matter that may enter the system. Like
hydraulic filters, air filters have a removable element and a built-in relief valve. The relief valve is designed to open and
bypass the air supply around the filter element in case the element becomes clogged. Some air filters are equipped with
a paper-type element which must be replaced periodically. Others have a screen mesh-type which requires periodic
cleaning. The screen mesh-type may be returned to the system after being cleaned and dried.
f.
Servicing Filters, Filters should be serviced in accordance with schedules and procedures contained In
technical manuals pertaining to the specific aircraft involved. However, the following general guidelines apply to the
servicing of all aircraft hydraulic system filters:
(1) Handle filters carefully. A hole no larger than a pinprick will permit large foreign particles to pass through
the element.
(2) Service filters in a clean area; this will help keep dirt and other foreign particles from entering the system
while the filter is being serviced.
(3) Do not leave a disassembled filter housing unprotected because this may cause contamination.
(4) Remove wrappings from a replacement element only when the element is to be inspected or installed.
(5) The filter bowl should only be hand tightened to the head. Always safety the bowl and head together
(6) Be sure that a popped-out Indicator button is indicating the need to service the filter. Push the button
back In with the system at normal operating pressure. If the button pops out again, the filter needs servicing; if It stays
in, the filter is not clogged.
4-13.
Pumps and Motors. The hydraulic pump is the mechanism for transferring and pressurizing aircraft hydraulic
fluid. Aircraft systems use engine-driven power pumps for this purpose. Hand pumps are also provided as emergency
equipment and for ground checking the hydraulic system. Hydraulic motors in Army aircraft perform such functions as
landing gear retraction and extension and operating cargo ramps, doors, and winch hoists.
a.
Power Pumps. The primary energizing unit of the hydraulic system is the power pump. It is the unit that
normally delivers hydraulic fluid under pressure to the actuators. Power pumps may be driven by an electric motor, a
turbine unit, or the aircraft engine; however, engine-driven pumps are used in all Army aircraft at this time. The piston
type power pumps used in modern hydraulic systems run at a rated speed of about 1 1/2 times engine crank-shaft speed.
In the drive shafts of all power pumps, there is a thinned portion that provides for a shearing action. If the pump seizes,
the shaft will break at this point, thus preventing damage to the engine or the transmission.
(1) Bent-axis constant-volume pumps. Constant-volume piston-type pumps put out a constant flow of fluid
for any given rpm. The pistons (usually seven or nine In number) are fastened by universal linkage to the drive shaft, as
shown in figure 4-101. The universal link (2) in the center drives the cylinder block (4). This block is held at an angle to
the drive shaft (1) by the housing. Pumps are available with different angles between the drive shaft and the cylinder
block; a large angle provides more output volume per revolution because the larger angle increases the piston stroke
(a) Theory of operation. Figure 4-102 illustrates the theory of operation. As the drive shaft (1) rotates the
cylinder block (4) and the piston assemblies, all the pistons are always the same distance from their points of attachment
(3) on the drive shaft Although the pistons appear to move within the cylinders, it Is actually the cylinders that move back
and forth around the pistons as the block and piston assembly rotates. Figure 4-103 shows a pump with pistons on intake
and pressure strokes. Piston (1) is at the top of its cylinder,
4-109
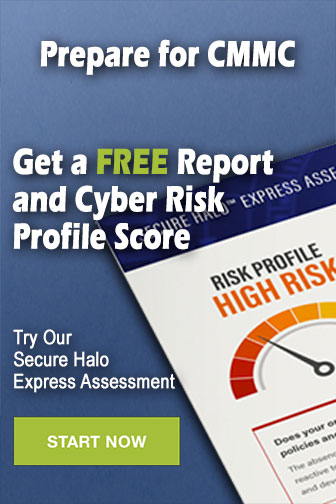