TM 1-1500-204-23-2
having just completed its pressure stroke and ready to being its intake stroke. As the block starts to rotate from this
point, the piston becomes aligned with the intake port (3). When the block has turned one-half of a revolution, the piston
reaches the bottom of the cylinder (4). The cylinder space formerly occupied by the piston is now full of fluid. As the
block continues to rotate, the piston becomes aligned with the outlet port (2) Having now moved through the last 180
degrees of rotation, it has exhausted all fluid from the cylinder and is ready to make another cycle. Since several pistons
are operating as described and since the cylinder block and piston assembly rotate rapidly, there are always pistons
somewhere between the upper and lower positions. This ensures a constant intake and output of fluid
(b) Cooling and lubrication. The piston-type pump uses case pressure for cooling and lubrication. Fluid
seeps by the pistons in the cylinder block and fills all the space inside the pump. This fluid cannot escape through the
drive end of the pump because of a seal around the drive shaft. Excess case pressure within the housing is routed back
to the intake side of the pump. This is done through a relief valve called a foot valve (figure 4-104). This valve prevents
the case pressure from rising above approximately 15 psi Drilled passageways through the universal link rods help to
keep the rod ball end lubricated
(2) Variable-volume pumps A variable volume pump has some advantages. One is that its use does away
with the need for a pressure regulator or an unloading valve Integral flow control valves regulate the pressure according
to the demands made on the system A second advantage is that pressure surges are reduced. Accumulators are not
needed to smooth out surges with systems using variable-volume pumps, but they are retained to aid the pump when
peak loads occur.
(a) Stratopower effective stroke pumps. As shown in figure 4-105, the drive shaft (1) rotates the cam (3).
This cam causes the nine spring-loaded pistons (4) to move back and forth in their cylinders, which are in a stationary
cylinder block. In operation, each piston is forced Into and removed from the cylinder once for each revolution of the
cam. The pistons are held in contact with the cam by piston springs, which also return the pistons after each forward or
power stroke Each piston has a half-ball bearing surface which acts like a universal linkage The flat side contacts the
cam during all angle changes. The pistons have fairly large hollow centers, connected with cross-drilled holes. Around
each piston there is a sleeve (5) attached to a spider (6), which in turn is attached to the compensator (7). An increase in
pressure moves the compensator to the right Decreased pressure allows it to move to the left because of the valve
spring tension. As the pistons travel to the left, fluid drawn from the inlet port (12) passes through the open center of the
cylinder block and then Into the cylinders (13) At this point, hydraulic fluid fills the center of the pistons. Some fluid will
continue to flow out through the cross-drilled holes and on to the pump return port (2) on the drive end of the pump. As
the pistons are forced to the right by the cam (3), the cross-drilled hole of each piston is blocked off by its sleeve About
the time that the cross-drilled passage is blocked off, the supply annulus (8) that surrounds the cylinder is also blocked
off. This condition traps the fluid in the piston and cylinder. As the piston continues on to the right, pressure builds up
against the check valve (10). Fluid under pressure goes out the check valve into the pressure chamber (9) and through
the outlet port (11). When the piston moves as far right as possible, the cycle starts all over again. This cycle is the
same for all nine pistons.
1 Zero flow. (See figure 4-106). As pressure rises in the pressure outlet line, it is also felt in the passageway
(14). This pressure acts on the compensator (7), forcing it to the right. This compresses the spring and carries the spider
and sleeves (6 and 5) with the compensator. The more the sleeves move to the right, the farther each piston travels
before the cross drilled passage is covered. This means that less fluid is trapped by the right end of the piston for output
to the pressure manifold. The maximum setting of the compensator is all the way to the right. Then the output to the
pressure manifold drops to zero, as shown In figure 4-106 In this condition, all intake of the pump goes out the return port
(2) Rotation of the cam draws fluid through the pump for cooling and lubrication There is always fluid being pumped
through the inlet port. But fluid will not be pumped through the outlet port until system pressure drops low enough to
demand it. Always connect the proper lines to the ports marked IN, OUT, and RETURN
2 Pressure regulation. The stratopower pump does not require a pressure regulator The compressor serves
nearly the same purpose Pressure can be increased by turning the adjusting screw (15, figure 4-106) clockwise or
decreased by turning it counterclockwise
(b) Vickers stroke-reduction pump. (See figure 4-107). The Vickers stroke-reduction pump operates
somewhat like the constant volume piston-
4-110
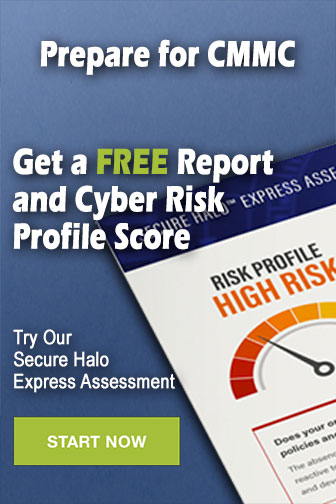