TM 55-4920-328-13
NOTE
The specified warmup and stabilization of the
power supplies will be accomplished during the
time
required
for
the
following
functional
checkout procedures.
r. Energize the following switchlight units on services
panel assembly 4A1 as shown in figure 1- 25.
ENGINE DC (27)
115 VAC 400HZ (28)
INST DC (29)
CONSOLE DC (30)
26 VAC 400 HZ (31)
s. Depress the LAMP TEST switchlight unit (24) on
services panel assembly 4A1 (9) and en- sure that all
switchlight unit lamps come on, then release the LAMP
TEST switchlight unit. All lamps must go off at this time.
t. Depress and hold the TEST switchlight unit
(26) and observe that all ALARM DISPLAY indicators (11
through 23) intermittently flash on and off and that the
audible alarm unit sounds continuously. Do not release
the TEST switchlight unit at this time.
u. While holding the TEST switchlight unit (26) in the
depressed position, depress and hold the ACK switchlight
unit (25). Observe that all indicators on the ALARM
DISPLAY section of the panel come on and remain on,
and that the audible alarm ceases to sound.
v. Release the TEST switchlight unit (26) and the ACK
switchlight unit (25). Observe that all indicators (11
through 23) go off and remain off when the switchlight
units are released.
w. Depress the LAMP TEST switchlight unit (17, figure 1-
24) on operator's panel assembly 3A3. Observe that all
switchlight unit lamps (16 through 30) come on.
x. Release the LAMP TEST switchlight unit (17). The
switchlight unit lamps must go off.
y. Energize the following switches on the No.. l power
control panel assembly (32, figure 1-26):
CAUTION
Energizing the BRAKE PUMP start switch (8)
causes large transient power VARIATIONS. The
Inst Pwr switch (7) should be OFF prior to
energizing the brake pump start switch, and then
energized
ON
after
the
pump
stablizes.
BRAKE PUMP START (8)
COOLING PUMP START (9)
TOWER FAN NO. 1 START (10)
TOWER FAN NO. 2 START (11)
AIR COMP START (12)
LUBE PUMP START (13) (if applicable)
OIL PRE-HEAT ON (14) (for T63 engine test only)
OIL PUMP START (15) (if applicable)
FUEL PUMP START (16)
FLOOD LIGHTS ON (17)
BEACON ON (19)
NOTE
The pressures specified in the following step
may be adjusted with the engine disconnected,
or with the engine connected but not operating.
z. For test of a T53 engine, adjust the pressure regulator
valve (76, figure 7-8) to a pressure of 10 + 0.5 psig as
indicated on the pressage gage (80). For test of a T63
engine, adjust the pressure regulator valve for a pressure
of 5 + 0.5 psig.
aa. Observe and record the ambient barometric pressure
indicated on the barometer (11, figure 1- 27) located on
the ancillary panel assembly 9A3
(37.
ab. Note and record the time of day indicated on the 24-
hour clock (5).
ac. Position the AIR SUPPLY switch (9) to ON.
ad. Adjust the pressure regulator (6) until the air pressure
gage (8) reads the pressure desired.
ae. Note the inlet and outlet pressures indicated on the
WATER PRESSURE IN meter M3 (4, figure 1-25) and on
the WATER PRESSURE OUT meter M4 (5) Ensure the
the water-in master control unit is partially open and that
the water-out master control unit is fully open. Refer to
figure 1-21 for the location of the master control units on
the for- ward writing surface assembly adjacent to the
operator's sub-module.
af. Adjust the master control unit as required to obtain 30
psig inlet water pressure to the remote water brake
assembly, as indicated on the WATER PRESSURE IN
meter (4, figure 1-25).
ag. Depress the following switches on the No. 1 power
control panel assembly (32, figure 1-26) to deenergize the
associated circuits:
2-48 Change 2
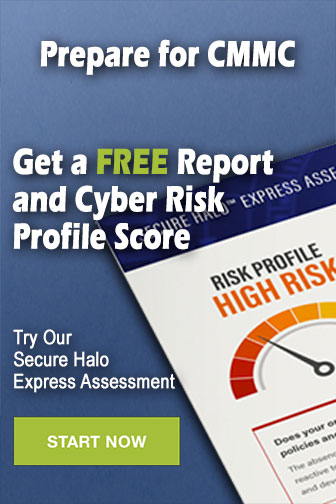