TM 55-920-328-13
(1) Electrically zero the appropriate torque indicators:
TORQUE/PRESSURE digital indicator (4, fig-ure 1-
22)
TORQUE PRESSURE indicator (2, figure 1-24)
T55-L-7 series torque indicator (2, figure 2-7)
T55-L-11/712 torque indicator (3, figure 2-7)
(2) Depress the R/CAL pushbutton switch on the
data selector assembly (7, figure 1-22). (This action will
drive the appropriate indicator upscale or provide a
display on the digital voltmeter type of instrumentation.)
The readout obtained must correspond to the R/CAL
factor established for the torque system being checked. If
the readout is not within the specified tolerance, calibrate
the torque system in accordance with the applicable
periodic procedures outlined in TB 55-4920-328-50 prior
to proceeding with the following checkout procedures.
The tolerances for the torque systems to be checked are
as follows:
T53 Turboprop Engines
+100 inch-pounds
T53 Turboshaft Engines
+50 inch-pounds
T55 Turboshaft Engines
f50 inch-pounds
T63 Turboshaft Engines
+25 inch-pounds
T74 Turboprop Engines
i50 inch-pounds
T73 Turboshaft Engines
±50 inch-pounds
T700 Turboshaft Engines
-+25 inch-pounds
an. Place the FUNCTION control (3, figure 1-23) in
TEST. The GAS PRODUCER speed monitor unit digital
indicator (1) must indicate 2381 + 1 for all engines except
T700 and 0468 will be the factor used, and repeat the
reading until the FUNCTION control setting is changed.
After verification of instrument self test, place the control
in RUN. The digital display unit will display all zeros,
unless there is an input signal from the remote sensor or
transducer.
a o. Place the FUNCTION control (8) in TEST. The
POWER TURBINE speed monitor unit digital indicator (6)
must continuously display 2381 1 for all engines except
T700 and 0750 will be the factor used, and re- peat the
reading until the FUNCTION control setting is changed.
After verification of instrument self test, place the control
in RUN. The digital display will indicate all zeros, unless
there is an input signal from the remote sensor or
transducer.
ap. Place the FUNCTION control (13) in TEST. The
OIL FLOW/CONSUMPTION monitor unit (11) must
display 1000 and repeat the reading until the FUNCTION
control setting is changed. After verification of self test,
place the control in RUN. The digital indicator will then
display a random read- out, depending on the input signal
from the oil quantity probe.
aq. Place the FUNCTION control (18) in TEST. The
FUEL FLOW monitor unit (16) must display the pre-set K
factor and repeat the reading until the FUNCTION control
setting is changed. After verification of self test, place the
control in RUN. The digital indicator will then display all
zeros, unless there is an input signal from the remote
transducer.
2-10. Multi-Channel Vibration Meter.
Functional check should be made of the multi- channel
vibration meter 2A3 (21, figure 1-23) prior to initial usage,
and prior to daily operation, in accordance with the
following:
NOTE
The following instructions are typical for each
channel in the unit.
a. Energize the METS electrical system as outlined in
paragraph 2-9.
b. Allow a 10-minute warmup and stabilization period
prior to adjustment of the multi-channel vibration meter.
NOTE
The following instructions must be accomplished
with
the
engine
accessories
vibration
transducers
electrically
connected
to
the
appropriate connectors on the data acquisition
assembly (unit 11). Refer to paragraphs 2-14
through 2-35 as applicable, for information on
interconnection instructions.
c. Verify that the on-off switch on the rear panel is in the
ON position.
NOTE
If the vibration pickup sensitivity is known,
proceed to step (g). If the sensitivity is
unknown, accomplish the entire procedures in
the following text.
d. Check to ensure that all channels of the unit are
electrically connected to the data acquisition assembly. If
the vibration pickups used in engine
Change 4 2-51
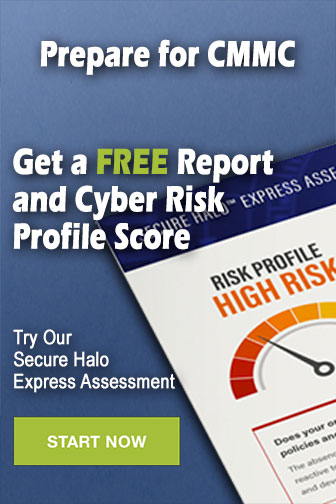