TM 55-4920-328-13
mechanical linkage. Pressure applied to the diaphragm
causes the rotor to move to vary the induced voltages
across the transformer (stator) output leads. Excitation
voltage for the unit is provided by system 26v ac, 400
Hz power. The input pressure range of the transmitter is
0 to 1,000 psig. A zero adjustment knob is located on
the rear face of the transmitter housing to provide an
electrical zero output at no input pressure. The ac
analog output is conditioned and displayed as gage
pressures on the TORQUE/ PRESSURE digital indicator
(4, figure 1-22). Selection of the pressure circuit
function to be displayed is made by depressing the
applicable pushbutton switch on the data selector
assembly (7).
11. TC/I Transmitters MT15 through MT19.
Five identical thermocouples to current (TC/I) low
temperature transmitter (238, figure 724) are installed in
the data acquisition assembly (Unit 11). Since these
components are identical, only one will be described.
The transmitter is a solid state modular measuring
circuit used to sense input voltages (in millivolts) from a
remote thermocouple. The unit converts the input to an
output current signal. This signal is transmitted to a
panel-mounted vertical scale indicator to provide display
of low temperatures sensed in the water brake assembly
subsystem. Input power for the transmitter is provided
by system 28v dc electrical power. The current drawn
from the input power source acts as the output signal.
TC/I transmitter MT15 senses inlet water temperatures
to the water brake assembly used as a power absorption
device during an engine test. Output of the transmitter
is displayed on the WATER TEMPERATURE IN meter
(2, figure 1-25). Transmitter MT16 senses outlet water
temperatures in the water brake assembly and displays
the
sensed
temperatures
on
the
WATER
TEMPERATURE OUT meter (3). Transmitters MT17,
MT18, and MT19 sense temperatures of the water brake
assembly bearing No. 1, bearing No. 2, and bearing
No. 3, respectively. These temperatures are displayed
on the No. 1 BEARING TEMPERATURE meter (6); No.
2 BEARING TEMPERATURE meter (7), and No. 3
BEARING TEMPERATURE meter (8), respectively.
12. Pressure
regulator.
The
pressure
regulator (224, figure 7-24) is a relieving-type pneumatic
regulator used in the T53 P1 air system.
The regulator is capable of regulation of inlet air
pressures up to 150 psig to outlet pressures from 0 to 20
inches H20.
13. Air pressure gage. The air pressure gage
(228, figure 7-24) is a diaphragm-operated, panel-
mounted, pneumatic gage used in the T53 P1 air
system during waveoff checks. The instrument is used
to display air pressures from 0 to 35 inches H20 in 1/2-
inch increments.
14. Solenoid valve. The solenoid valve (232,
figure 7-24) is an electrically-operated valve used in the
T53 P1 air system. Electrical power for operation of the
valve is supplied by system 28v dc power, through the
P1 AIR switchlight unit (27, figure 1-24) on the
operator's panel assembly. Supply air at approximately
125 psig, downstream from the right hand castle
assembly (Unit 9), is routed through the solenoid valve
and pressure regulator in the data acquisition assembly
to the P1 AIR OUT quick-disconnect coupler (12, figure
1-29). Connection to the coupler on the data acquisition
assembly may be made to connect the P1 bellows on
the T53 engine fuel control.
e.
Auxiliary trailer assembly. The auxiliary trailer
assembly (figure 1-31) consists of the auxiliary trailer
module (figure 1-32), cooling tower module (figure 1-
36), and diesel engine ac generator and cable set (figure
7-31). The auxiliary trailer assembly provides a
continuous supply of water to water brake assemblies,
water brake bearings, and for cooling lubricating oil.
The cooling tower module, which cools the returning
water, is capable of dissipating heat energy equivalent
to 5,000 horsepower on a standard 85 °F wet bulb day.
The diesel engine ac generator and cable set supplies
all of the electrical power required for METS operation.
Refer to paragraph 15 for leading particulars of the
auxiliary trailer assembly.
(1) Auxiliary
trailer
module.
The
auxiliary trailer module (figure 1-32) consists of a frame
and running gear assembly (1), water system (3), power
distribution box (2), forward and aft leveling jacks (4,8),
deck plates (7), storage boxes (5,6), and associated
piping, cabling, and hardware. The forward and aft
leveling jacks provide leveling adjustment of the
auxiliary trailer. The leveling jacks can withstand side
loads resulting from uneven terrain or off-center loading.
Each forward leveling jack is trunnion-mounted and
swings upward to attach horizontally beneath the
auxiliary trailer. Each aft leveling jack has an adjustable
clamp bracket that may be adjusted along the entire
length of the jack tube toward the gear head. The right
and left deck plates (7) encompass the area around the
water
pumps
and
power
1-62
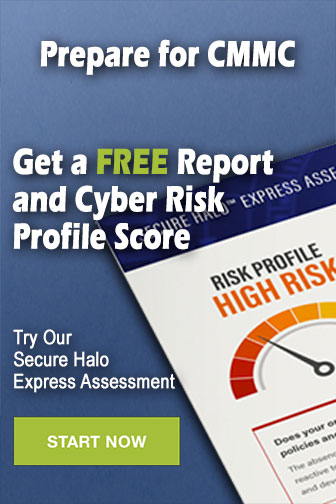