TM 55-4920-328-13
a 30-foot long interconnecting hose assembly, to the test
trailer water system. Refer to paragraph 14e(2) for
information on the cooling tower module. With system
power available from the generator set, the following
circuit breakers in the power distribution box on the
auxiliary trailer assembly are closed to make available
208v ac, 60 Hz, three-phase power to the four motors in
the water system:
Water Brake Pump CB1
Tower Fan CB2
Tower Fan CB3
Tower Pump CB4
The INST PWR ON switch (7, figure 1-26) is then
depressed to energize the No. 2 power control panel
circuits. Under this condition, the BRAKE PUMP
START switch (8), COOLING PUMP START switch (9),
TOWER FAN No. 1 switch (10), and TOWER FAN No.
2 switch (11) are then depressed to energize the coils of
relays K1 through K4 in the water system circuitry.
Energizing the relays applies electrical power to the
respective motors in the water system. The system is
deenergized in reverse order.
(c)
Auxiliary trailer power distribution box.
The auxiliary trailer power distribution box (2, figure 1-
32) is located on the aft right side of the auxiliary trailer
module above the trailer deck. The power distribution
box
is
a
rectangular
sheet
metal
enclosure
approximately 48 inches high, 20 inches wide, and 8
inches deep. The power distribution box is provided
with knock-outs on the side and bottom panels, and has
two connectors on the lower front panel. One connector
J1, identified CONTROL, is used to interconnect the
power distribution box with the control circuits in the
control cab module. The second connector J2,
placarded POWER OUT, is used for interconnection of
internal components with other control and indicating
circuits in the control cab module. Three-phase, four-
wire, 208v ac, 60 Hz power from the generator set is
routed to the power distribution box. (See figure 7-31.)
Connection is made within the unit at four busses: OA,
OB, OC, and GRD. Four of the five circuit breakers
within the unit, CB1 through CB4, are used to connect
the primary power source to heavy-duty, motor starters
K1 through K4. The fifth circuit breaker CB5 supplies
primary 208v ac power to the test trailer assembly.
Motor starters K1 through K4 are identical in design and
function except for the associated circuitry. Each unit
consists of two normally-closed sets of contacts, three
normally-open sets of contacts, thermal overload
protective elements, and a coil. These thermal
elements are connected in series with the three-phase
power circuits to the motors in the water system. The
normally-closed pair of contacts in series with the relay
coil open on an overload to deenergize the relay. The
other normally closed set of contacts open when the
relay coil is energized and close when the coil is
deenergized.
When this pair of contacts opens during system
operation, the associated interlock circuit causes a
SERVICES INOPERATIVE alarm and shuts down the
engine. Motor starters K1 and K4 are used in the alarm
circuits. The four units, identified by reference
designation, are used in the following circuits:
K1 Water System Water Brake Pump Motor
K2 Water System Tower Fan No. 1 Motor
K3 Water System Tower Fan No. 2 Motor
K4 Water System Tower Pump Motor
(2)
Cooling tower module. The cooling tower
module (figure 1-36) is a centrifugal fan blowthrough
unit which dissipates heat from the water being
discharged from the water brake assembly.
The cooling tower module operates as a part of the
auxiliary trailer water system. The cooling tower module
is located behind the water tanks on the auxiliary trailer
assembly. (See figure 131.) The cooling tower module
consists of a blower section (8, figure 1-36), two 7-1/2
horsepower fan motors (5) and drives, and a heat
transfer section (1). The blower section is a
combination drain pan and fan arrangement consisting
of a vee-shaped sump, blow-through centrifugla fans (6)
and a heavy supporting angle framework. Three parallel
fans and one motor are mounted on each side of the
sump. The six fans develop a converging high velocity
discharge column of air which rises above the cooling
tower module before dissipating into the atmosphere.
The air discharge pattern prevents recirculation of
warm, moist, discharge air back to the fan intakes to
prevent reduction in cooling tower performance. The
vee-shaped construction makes the pan self-cleaning;
foreign matter drops to the bottom by the water flowing
down the pan sides. Discharge cowls in the pan give
the cooling tower module optimum fan performance and
air distribution through the heat transfer surface. In
addition, the cowls prevent falling water from entering
the fans. Circular access doors provide easy entry to
pan interiors. Removable screens (7) permit access to
moving parts in the fan assembly. The fan motors,
drives, and bearings are located under the sloping pan
sides for protection from the elements. A sliding motor
mount permits easy vee-belt tension adjustment. The
heat transfer section
1-67
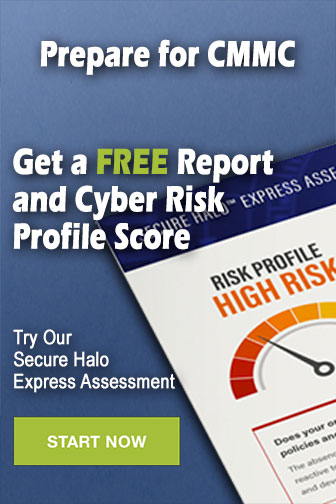