TM 1-1500-204-23-6
(6)
Checking torque. Checking installed
fasteners to determine if they have been tightened to
the specified torque value cannot be accurately
accomplished using a torque wrench. Installed
fasteners generally require more torque than was
originally applied, in order to overcome static friction
and start the fastener turning. To ensure proper torque
has been applied, the fastener should be backed off
from one-half to one full turn and retightened to the
correct torque value. A torque wrench should not be
used for the backoff operation.
(7)
Retorquing.
In
some
special
applications, it is necessary to retorque a fastener after
a prescribed period following initial installation in order
to insure that proper clamping force and bolt tension are
still in effect. If retorquing is required, the applicable
aircraft maintenance manual should be consulted for
proper retorquing procedure.
(8)
Damaged
threads.
Studs
with
damaged threads should be replaced or the threads
rechecked; however, this is not always possible in field
maintenance. To overcome the problem of tightening a
nut on a stud to the proper torque value where thread
damage is present and therefore increases the rundown
resistance of the nut, add the rundown resistance to the
specified torque value. The rundown resistance should
be measured on the last rotation before the nut seats.
For example, if 325 inch-pounds of torque is specified
for an application and the rundown resistance due to
thread damage is 25 inch-pounds, the nut should be
tightened to a torque of 325 inch-pounds plus 25 inch-
pounds, or 350.
c. Recommended
Torque
Values.
For
recommended torque values, refer to tables 2-8 and 2-9.
2-19. Safety Cable.
a.
General Instructions for the Selection of
Safety Cable. The selection of materials shall be in
accordance with AS4536 (SAE), available from SAE
International, 400 Commonwealth Avenue, Warrendale,
PA 15096-0001, and shall be in accordance with the
service limitations outlined herein.
NOTE
Minimize mixing of safety wire and
safety cable.
(1)
AS3510 series (UNS S32100 CRES)
safety cable shall be selected for general purpose use
on all applications up to 649 °C (1200°F).
(2)
AS3509 series (UNS N6600 Nickel
Alloy) safety cable shall be selected for up to 9820C
(18000 F).
(3)
Only
safety
cables
and
ferrules
supplied by a manufacturer that meets all the
requirements of AS4536 shall be allowed.
(4)
Safety cable shall not be used for any
shear, or break away applications.
(5)
Safety cable shall be installed with a
calibrated tool which is supplied by the safety cable
manufacturer
for
the
purpose
of
applying
a
predetermined cable tension, crimping the ferrule, and
cutting the excess cable without allowing tension to be
lost.
b.
The Size of Safety Cable Shall be in
Accordance with the Following Requirements:
(1)
0.020 inch diameter safety cable is
intended for use on parts having a nominal hole
diameter of 0.045 inch (1.14 mm) or smaller.
(2)
0.032 inch diameter safety cable is
intended for use on parts having a nominal hole
diameter of 0.075 inch (1.91 mm) or smaller.
(3)
0.040 inch diameter safety cable is
intended for use on parts having a nominal hole
diameter of 0.095 inch (2.41 mm) or smaller.
(4)
The specified length of the cable shall
be selected to accommodate the span between
fasteners added to the length of cable required to
correctly engage the application tool.
(5)
Applications where safety cable is to be
installed through a hole having a nominal diameter of
greater than 0.095 inch (2.41 mm), but less than 0.200
inch (5.08 mm) shall require a flat washer (same
material composition as the safety cable) which is
supplied by the manufacturer for this purpose, and shall
be used as shown in figure 2-83.
Figure 2-83. Flat Washer Safety Cable Installation
(FW10-1)
(6)
Safety cable shall be installed with an
application tool which has been calibrated to meet the
performance requirements of AS4536 (SAE) and this
manual.
Change 2 2-84
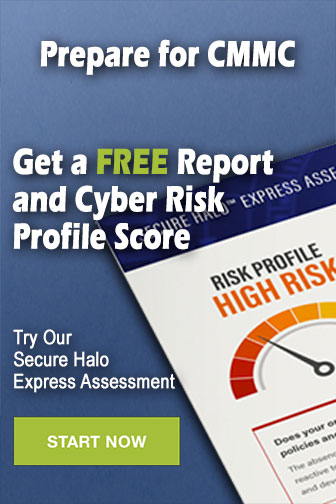